Fuel Distribution
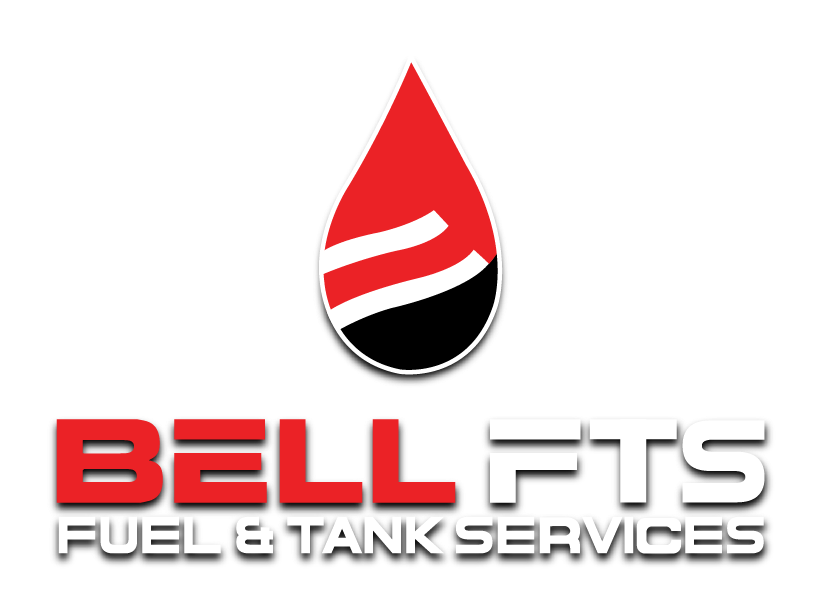
Bell Fuel & Tank Services: Serving Fuel Distributors
A fuel distributor’s business revolves around delivering in-spec product to their customers, when they need it. Their customers expect fuel that meets specifications and doesn’t give them problems. That’s not too much to expect.
Changes to today’s fuel can make meeting these expectations a challenge at times. They must overcome this challenge or face losing credibility with their customer or, worse, being viewed as a cause of their problems.
Today’s fuels are not what they used to be. The fuel may be in-spec when it comes from the refinery, but it’s also prone to developing microbe and water problems much more quickly than the fuels of before.
For these and other reasons, Bell Fuel & Tank Services (Bell FTS) offers the right tools and the right approach to support fuel distributors and help them reach their goals.
The Hybrid Approach for Fuel Care
Bell Fuel & Tank Services works with fuel distributors to offer a different way of best-practice fuel management - the Hybrid Approach to fuel care. For fuel distributors, it's the best way of keeping fuel and storage tank issues out of their hands, ensuring the fuels they send out to their customers stay fuel-problem-free and ready for business.
Bell Fuel & Tank Services partners with fuel distributors to help them stay problem-free with the best fuel treatment chemistries that prevent serious problems with microbes and MIC tank corrosion, ensuring their important customers stay problem-free as well. Bell Fuel & Tank Services also provides the best mechanical tank services and fuel problem mediation, to cover the elements of fuel health that fuel treatment chemicals can’t achieve.
Just as importantly, both of these essential elements are supported by state-of-the-art testing and monitoring that ensure that fuel distributors know what’s going on with the condition of their tanks and the product that’s going out. This includes next-generation microbe detection testing that can give a fuel distributor critical information about microbial fuel contamination (or the potential thereof) which is impossible to know otherwise.
This best practice approach to fuel PM helps fuel distributors predict and head off problems instead of reacting to them. And this helps keep their customers problem-free as well.
Helpful Resources
What's My Fuel Health Score?
Webinar
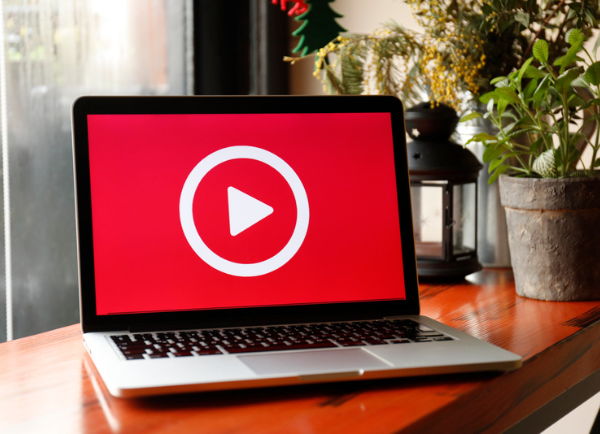
Fuel Changes and How They Affect You
Webinar
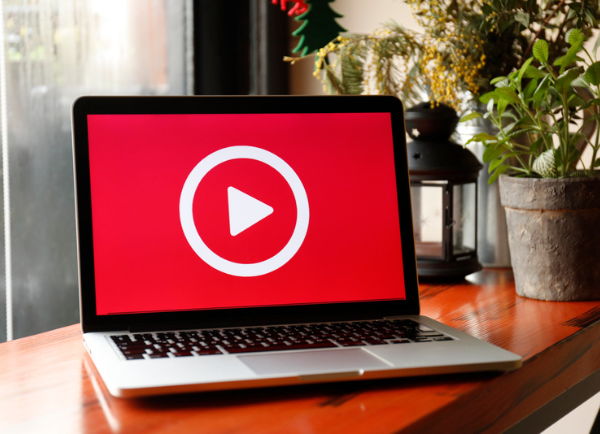
Top Ways Microbes Cause Fuel Headaches for Fuel Distributors
Technical Sheet
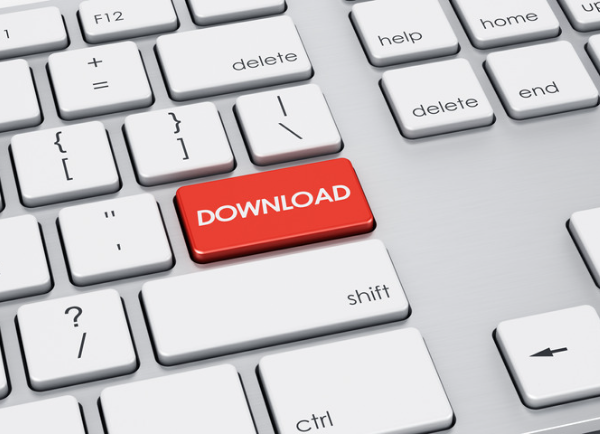
Essential Fuel Tests
Tip Sheet
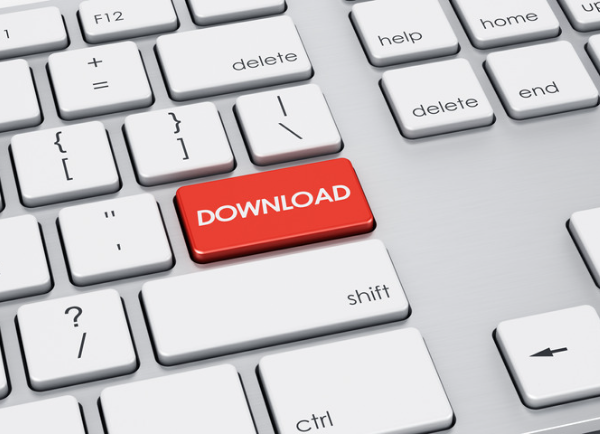
How To Prevent Diesel Fuel Microbes
Whitepaper
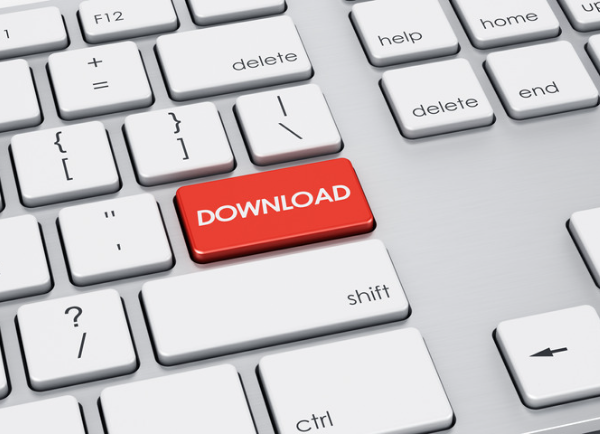
Tank Partners Checklist
Checklist
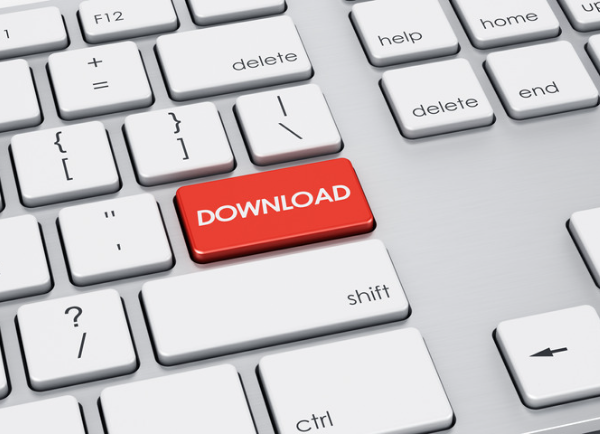
Storing and Dispensing Fuel
Webinar
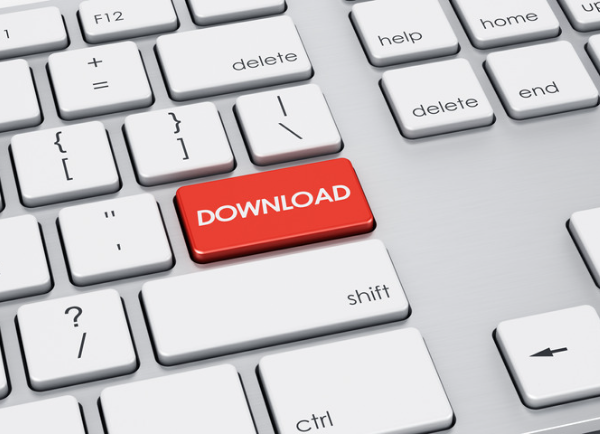