Data Centers
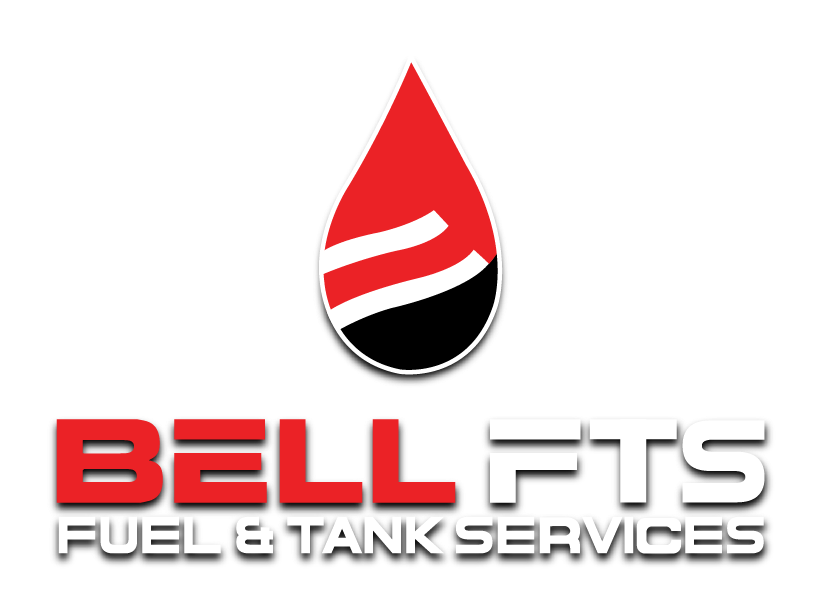
Data Center Generator Fuel Quality: The Complete Guide to Preventing Backup Power Failures
Data center operators invest millions in redundant power systems, yet many overlook the most critical component: fuel quality. When the grid fails and your diesel generators kick in, contaminated or degraded fuel can turn your backup power into a liability. Understanding fuel quality management isn't just about maintenance—it's about ensuring business continuity when every second of downtime costs thousands.
Why Data Center Generator Fuel Quality Matters More Than Ever
The stakes have never been higher for data center uptime. Modern facilities support everything from cloud computing to AI workloads, where even brief power interruptions can cascade into major outages. Yet according to industry data, 20% of emergency backup systems failed during the 2003 Northeast blackout, specifically due to fuel-related problems—not mechanical failures, but degraded diesel that couldn't sustain generator operation when needed most.
The financial impact extends beyond immediate downtime costs. Misdiagnosing fuel problems often leads to unnecessary component replacements. Fuel injection pump replacements can cost $5,000 or more per generator, while incorrectly disposing of "bad" fuel—often perfectly usable diesel—can incur disposal fees ranging from $5 to $20 per gallon, plus replacement costs.
The Hidden Enemies of Stored Diesel Fuel
Microbial Contamination: The Silent Killer
Microbial contamination represents the single most damaging threat to stored generator fuel. Bacteria and fungi don't just consume your diesel—they create acidic byproducts that accelerate fuel degradation and tank corrosion while producing biomass that clogs filters and injection systems.
These microorganisms thrive in the interface between fuel and water, which explains why water management becomes so critical. Even trace amounts of water can support microbial colonies that multiply rapidly in warm storage conditions typical of data center environments.
Signs of microbial contamination include:
- Black, slimy residue in fuel filters
- Distinct sour or rotten odors from fuel samples
- "Leopard spotting" on filter media indicating microbial colonies
- Cloudy or milky appearance in fuel
- Organic clumps or particles in separated water
To combat ths problem, try Bellicide or ClearKill.
Fuel Oxidation and Chemical Breakdown
Stored diesel fuel naturally degrades over time through oxidation processes that accelerate in the presence of heat, light, and catalytic metals. This breakdown produces gums, varnishes, and heavy sludge compounds that settle in tank bottoms and create deposits throughout the fuel system.
The oxidation process becomes self-perpetuating as degradation products catalyze further breakdown. What starts as slight fuel darkening can progress to complete fuel stratification, where heavier compounds separate and become unpumpable sludge.
To combat ths problem, try Dee-Zol Life.
Cold Weather Gelling
Data centers operating in colder climates al;so have to be concerned with gelling of their diesel fuel. This can shut operations down at critical times in the winter.
To combat ths problem, try Cold Flow Improver.
Water Accumulation and Phase Separation
Water enters fuel systems through condensation, tank breathing, and contaminated fuel deliveries. Beyond supporting microbial growth, water causes several direct problems:
- Ethanol blend phase separation: In mixed fuel systems using ethanol-gasoline blends for smaller generators, water causes permanent phase separation that renders fuel unusable
- Corrosion acceleration: Water promotes electrochemical corrosion of tank walls and fuel system components
- Fuel pump cavitation: Free water in fuel lines can cause pump damage during operation
To combat ths problem, try Ethanol Defense.
Essential Fuel Quality Testing for Data Centers
ASTM D-975 Compliance Testing
All stored diesel fuel should meet ASTM D-975 specifications, but which tests matter most for generator applications?
- Cetane Index (ASTM D-976): Measures fuel ignition quality. Generator fuel stored for extended periods often experiences cetane degradation that affects starting reliability and load-carrying capacity. Cetane deficiency manifests as hard starting, rough idle, and reduced power output—exactly what you don't want during an emergency.
- Fuel Stability (ASTM D-2274): This accelerated aging test predicts how fuel will behave in long-term storage. Samples are heated and exposed to oxygen to simulate storage conditions, with insoluble formation measured as an indicator of stability. Unstable fuel produces higher quantities of insolubles that translate to filter plugging and injector deposits in real-world use.
- Sulfur Content (ASTM D-2622): Ultra-low sulfur diesel (ULSD) requirements mandate sulfur content below 15 ppm. Exceeding this threshold creates legal compliance issues and can damage diesel particulate filter (DPF) systems in newer generators, leading to costly maintenance issues.
Water and Sediment Analysis (ASTM D-2709)
This centrifuge test measures both water content and sediment levels in fuel samples. Healthy diesel fuel should contain less than 0.05% combined water and sediment. Higher levels indicate contamination that requires immediate attention through fuel cleaning or polishing.
Microbial Testing Protocols
Regular microbial monitoring represents your first line of defense against contamination. While there are several options for testing technology, we believe the best one is:
- ATP-By-Filtration (Adenosine Triphosphate) Testing: Provides rapid, semi-quantitative results indicating total microbial activity in fuel samples. ATP tests can be performed on-site and give immediate feedback on contamination levels.
Comprehensive Fuel Management Strategies
Chemical Treatment Programs
Effective fuel preservation requires targeted chemical treatments based on specific fuel conditions and storage environments.
- Fuel Stabilizers: Antioxidant packages that prevent gum and varnish formation by interrupting oxidation chain reactions. Modern stabilizers can extend storage life from 6-12 months to 2-3 years when properly applied.
- Biocides: EPA-registered antimicrobial treatments that eliminate bacteria and fungi in fuel systems. Biocide applications typically use treat ratios between 1:2,000 and 1:10,000 depending on contamination severity. Shock treatments for active infections require higher concentrations than maintenance dosing for prevention.
- Water Controllers: Chemical treatments that either absorb dissolved water or modify fuel-water interfaces to prevent microbial establishment. These treatments work synergistically with biocides for comprehensive contamination control.
- Sludge Dispersants: Specialized chemistry that breaks down existing fuel sludge and biomass deposits, allowing mechanical removal through filtration or fuel polishing.
Mechanical Fuel Cleaning
Some fuel problems require mechanical intervention rather than chemical treatment alone.
- Fuel Polishing: Mechanical filtration systems that remove water, sediment, and microbial biomass from stored fuel. Polishing systems typically incorporate water separation, particulate filtration, and sometimes heating to improve separation efficiency.
- Tank Cleaning: Physical removal of sludge and biomass from tank bottoms and walls. This often requires fuel transfer to temporary storage while tanks undergo cleaning and inspection.
The Hybrid Approach
The most effective fuel management programs combine chemical and mechanical methods based on specific contamination types:
- Microbial contamination: Biocide treatment followed by filtration to remove dead biomass
- Water and sediment: Mechanical removal followed by chemical water control
- Fuel instability: Polishing to remove existing degradation products, then stabilizer treatment
- Tank sludge: Chemical dispersant application combined with mechanical cleaning
Implementing a Proactive Fuel Management Program
Regular Testing Schedules
Establish testing frequencies based on fuel criticality and storage conditions:
- Annual comprehensive testing: Full ASTM specification suite for all generator fuel systems
- Quarterly microbial monitoring: ATP or culture-based testing to detect contamination trends
- Monthly visual inspections: Tank gauging, water level checks, and sensory evaluation
Emergency Response Protocols
When generators fail to start, systematic diagnosis prevents costly misrepair:
- Fuel system inspection: Check filters for contamination signs before assuming fuel problems
- Mechanical verification: Confirm that fuel lines, valves, and pumps function properly
- Fuel testing: Submit samples for laboratory analysis before disposing of suspected "bad" fuel
- Expert consultation: Engage fuel specialists who understand both mechanical and fuel chemistry aspects
Documentation and Trending
Maintain detailed records of fuel testing results, treatment applications, and performance issues. Trending data helps identify patterns and optimize treatment schedules while providing documentation for compliance audits.
Cost-Effective Implementation
Partnership Benefits
Working with fuel management specialists offers several advantages over in-house programs:
- Laboratory relationships: Established partnerships can reduce testing costs by 50-70% compared to a la carte pricing
- Technical expertise: Access to fuel chemistry knowledge that prevents misdiagnosis and unnecessary treatments
- Regulatory compliance: Ensuring proper handling of biocides and waste fuel disposal
Subscription-Based Monitoring
Consider fuel monitoring subscriptions that provide regular testing and expert recommendations. These programs typically cost $875-$1,475 annually per tank but offer significant value compared to emergency response costs.
Return on Investment
Comprehensive fuel management programs typically pay for themselves through:
- Avoided disposal costs: Preventing unnecessary fuel replacement saves $5-$20 per gallon
- Reduced component replacement: Proper fuel maintenance prevents injector and pump failures costing thousands per incident
- Extended fuel storage life: Chemical treatments can double or triple usable storage periods
Regulatory Considerations and Best Practices
Environmental Compliance
Fuel management activities must comply with various environmental regulations:
- Biocide applications: Must use EPA-registered products applied according to label requirements
- Waste fuel disposal: Requires licensed disposal companies following DOT and EPA guidelines
- Spill prevention: Secondary containment and spill response procedures for fuel handling
Industry Standards
Several industry standards provide guidance for fuel management:
- NFPA 110: Standard for Emergency and Standby Power Systems includes fuel quality requirements
- Joint Commission standards: Healthcare facilities must demonstrate fuel readiness for emergency generators
- ASTM D-975: Defines specification limits for diesel fuel quality parameters
Common Mistakes to Avoid
- Over-reliance on Visual Inspection: Fuel can appear clean while harboring significant contamination
- Improper Sampling Techniques: Top-level samples may miss contaminants near tank bottoms
- Reactive vs. Proactive Approaches: Waiting for failure before acting is costlier
- Misunderstanding Additive Chemistry: Know the limits of stabilizers, biocides, and dispersants
Future Trends in Fuel Management
Advanced Monitoring Technologies
- Real-time sensors: Track water content and microbial activity continuously
- IoT integration: Remote access and alerts via facility platforms
- Predictive analytics: Machine learning anticipates degradation trends
Alternative Fuel Considerations
- Biodiesel blends: Require special handling and storage strategies
- Synthetic fuels: May offer longer shelf life
- Hybrid systems: Fuel cells and other tech introduce new requirements
Conclusion: Ensuring Reliable Backup Power
Data center generator fuel quality management represents a critical but often overlooked aspect of facility operations. The consequences of fuel-related generator failures extend far beyond immediate repair costs to encompass business continuity, regulatory compliance, and customer confidence.
Successful programs combine regular testing, appropriate chemical treatments, mechanical cleaning when needed, and partnerships with fuel management experts. The investment in comprehensive fuel management pays dividends through improved reliability, extended equipment life, and reduced emergency response costs.
Remember, when the grid fails and your generators are called into action, fuel quality becomes the difference between seamless backup power operation and catastrophic system failure. The time to address fuel quality isn't during an emergency—it's during the months and years of preparation that precede it.
For data center operators serious about uptime guarantees, fuel quality management isn't optional—it's fundamental infrastructure maintenance that deserves the same attention as UPS systems, cooling infrastructure, and network redundancy.
For expert consultation on data center fuel management programs, contact fuel specialists who understand both the technical requirements and business implications of reliable backup power systems.