The Complete Story Of Fuel Contamination
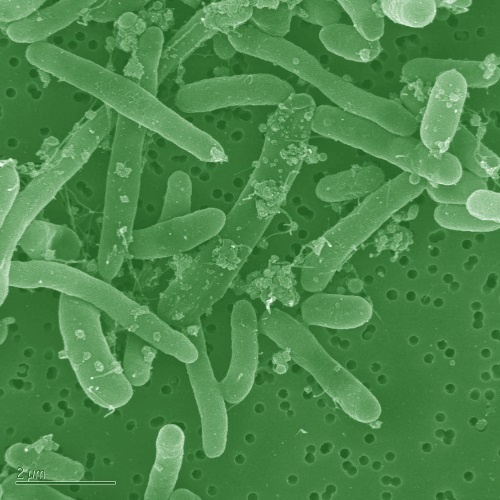
Fuel storage is vital for business and government but often overlooked. Diesel, stashed in tanks, generators, and emergency systems, waits for its crucial moment of use. It's assumed that when required, this fuel will function as intended, powering engines and systems effectively.
When fuel fails, the surprise is genuine. In emergencies, it's the leading reason for equipment malfunction. A deeper look reveals diesel contamination as a central concern requiring attention and accountability.
Address diesel contamination and you can prevent a lot of headaches. But it's a broad umbrella with lots of interralted things to consider.
Fuel Contamination – Fuels and Engines Have Changed
The fuel landscape has transformed due to various reasons. Enhanced environmental regulations have introduced fuels needing more maintenance. Updated engine designs, complying with stricter emission standards, demand higher fuel purity. These all underscore the increasing importance of managing fuel contamination.
Kinds of Diesel Fuel Contamination
Contemporary fuels face three primary contamination concerns: water, inorganic debris (like sand and rust), and organic debris (from fuel degradation and microbial byproducts). These form the common contaminants in fuels.
Often, people mislabel microbial contamination as "diesel fuel algae." However, it's less about "algae" and more about petroleum residues like gums and varnishes. True algae requires light, so it doesn't grow in tanks. Yet, other microbes such as bacteria, molds, and fungi thrive and can cause issues in stored fuel.
How The Fuel Itself Has Changed
Fuel management and operations professionals who have been in the industry for a long time can readily see that there’s something fundamentally different about today’s fuels vs. the fuels from decades past. If they can’t see it in the fuel itself, they definitely see it in the problems that develop more readily than before. It’s important to have a clear understanding of how fuels have changed if you’re going to understand these fuel contamination problems and what to do about them.
Change #1: Fuel used to have longer storage life
Historically, fuel had a longer storage life. In the 1960s, a US Army study found gasoline could last 2-5 years, while diesel fuel might remain stable for over a decade. Today, the scenario has shifted dramatically. Common gasoline (E10) has a shelf life of just 90 days, and Diesel Fuel #2 quality can degrade by 26% within the first 28 days. This degradation can rise to 95% if water is present.
What's responsible for this change? Refineries, due to increasing demand, have adopted newer methods to extract more fuel from the same crude volume. Techniques like hydrocracking break larger molecules in crude into smaller ones, maximizing fuel yield. As a result, we obtain more gasoline and diesel from each crude oil barrel. However, there's a downside: these fuels are less stable. They begin with a high content of "unstable precursors" – molecules that eventually transform into sludge, gums, deposits, and varnishes.
Change #2: ULSD, Water and Microbes
The move towards ultra-low sulfur diesel fuel (ULSD) in the last ten years has been great for the environment. Millions of tons of sulfur gases have been prevented from entering the atmosphere, and that’s good for things like preventing acid rain. But these ULSD fuels attract more water and are less resistant to microbes than the higher sulfur diesel fuels from before 2006. So when you’re linking this to the issue of fuel contamination, this fuel change means that today’s diesel fuels are far more likely to develop contaminants like microbes, biomass, sludge and water.
Stored Fuel Doesn’t Tend To Be Checked
With these considerations in mind, consider all those thousands of old stored fuel tanks scattered across the country. Some have partial or trace amounts of old diesel fuel in them, and many of those have had newer ULSD added to them. Stored fuel like this doesn’t tend to be checked until there’s an apparent or urgent need to do so – like the threat of a major hurricane.
What do you think’s going to happen with those tanks and the fuel when we get the next hurricane blitz? They’ll go to use the fuel and find some serious fuel contamination problems.
Common Fuel Contaminants: Water
Water accumulation in diesel tanks is a widespread issue nationally. Any stored diesel will likely have water settled at its base, especially with the evolving properties of ULSD fuels, intensifying the problem from yesteryears.
But how does water penetrate these fuel storage systems? Multiple routes exist. One primary way is through tank vents. However, unlike particle contamination, water's entrance isn't dictated by the fuel level. Instead, it's influenced by environmental shifts, such as temperature and humidity. Ambient air, laden with water vapor, circulates in and out of tanks. Within storage containers, atmospheric water condenses, sliding down tank walls as temperatures drop during evenings.
Interestingly, diesel engines contribute to the water problem. In diesel-powered vehicles, this arises from the hot diesel being rerouted to the tank after cooling injectors. Given injectors' immense pressures, they overheat, and diesel from the tank is employed to offset this heat. Upon cooling, the circulated hot fuel leads to water condensation within the vehicle tank.
Modern fuels have an affinity for retaining water. The trend of integrating minimal biodiesel into traditional diesel escalates water issues due to biodiesel's hygroscopic nature. Another factor is ultra-low sulfur diesel's lack of natural lubricants, replaced by lubricity additives. These additives enhance fuel surfactancy, inadvertently stabilizing water within the fuel. Essentially, these agents make it easier for water to mix with diesel, resulting in emulsification.
So why does water matter?
It matters, for the following reasons:
- Water allowed to accumulate in a tank increases the chance of a microbial infestation – bacteria and fungi which can play havoc with the fuel system.
- Water in fuel accelerates the oxidation and break down of the fuel.
- Water contamination contributes to tank corrosion
Water buildup in storage tanks needs control, typically via concentrated fuel treatment. However, if water levels are significant, it's wise to pump it out as part of a fuel PM strategy. While premium chemical water-controllers are beneficial, they have their limits. The ideal action largely depends on the tank's size and water content, making an informed partner invaluable.
Water in fuel exists in three states: free, dissolved, and emulsified. Dissolved water is spread molecule by molecule in the fuel, and standard diesel can hold up to 200 ppm of dissolved water. If water exceeds this threshold, it forms a fuel-water emulsion with minute water droplets suspended in the fuel. Beyond this, water transitions into free water, settling as a distinct layer in the tank's base.
Water contamination in fuel can vary significantly. Lab results often indicate ULSD fuel having water saturation near 50 ppm at 50° and about 200 ppm at 100°. This translates to 1.7 ounces of water dissolved per one hundred gallons of fuel. When tank fuel and its airspace cool to 50°, the fuel's water-holding capacity reverts to its original level, making the excess water either free or emulsified within the tank.
Common Diesel Fuel Contaminants: Microbes
Fuel Microbe Contaminants: Plugging Filters & Spreading The Problem
Microbes grow in the fuel tank, multiply, and produce biomass and slime growths which will plug filters in the storage tank. So, if you’re a fuel or tank manager and you notice an increase in the rate of filter changes needed, that’s one sign you need to look closer at what’s happening in your tank.
But this isn’t the only thing to be concerned about. The problem is easily spread to vehicles and other tanks through fuel transfer. This is another reason why it’s important to deal with the problem when you find it. If it spreads to things like vehicles and equipment, filter plugging issue becomes a real problem because this shuts down the vehicle or engine, which takes the machine out of commission, and depending on what you need it to do, an extra added expense and headache.
The Link To Fuel Instability
The Link To Microbe-Related Corrosion In Storage Tanks
The last major problem we see centers on microbial presence in fuel systems over a long period of time being strongly associated with corrosion damage in storage tanks, commonly called microbially-influenced corrosion or MIC.
In these scenarios, biological acid production from microbes attack and damage metal surfaces. Or they cause cathodic corrosion as they grow and flourish behind the protection of biomass formations. Some kinds of bacteria have been known to perforate a 5mm thickness of 316 steel in little more than one month. This may be a rather extreme case, but it does serve to illustrate that microbial corrosion can cause serious damage in shorter time than you might think. This damage is expensive and needs to be repaired when it happens, often running into the thousands per tank. If you’re in charge of purchasing or maintaining storage tanks, you know the scale of expense that we’re talking about.
Common Fuel Contaminants: Sludge and Particulates
Sludge buildup happens because diesel fuel forms heavy polymers that drop out and collect at the bottom of the tank, resulting in a sludge buildup in the storage tank itself.
This is a problem because, first, sludge like this represents energy value that’s not contributing when the fuel is burned. And second, sludge can plug filters and contribute to engine deposits if it happens to be consumed by another piece of equipment.
Organic contaminants in ultra low sulfur diesel can damage elastomer fuel filter seals and shorten fuel filter life. In this case, the organic contaminants are the result of free radical reactions in the diesel fuel. These reactions are accelerated in ultra low sulfur fuel due to the removal of naturally occurring antioxidants during the hydrotreating process for sulfur removal. As a result, a large number of peroxide molecules are generated. These peroxides promote oxidation and polymerization reactions and have a damaging effect on elastomer seals in fuel systems.
Particles in Fuel
Preventing Diesel Fuel Contamination
The storage problems that ultra-low sulfur diesel fuels experience mean it is more important than ever before for businesses, emergency backup and fuel storage entities to keep preventive maintenance in mind for their fuels. Today’s diesel fuels have enough problems that they cannot risk their fuel not performing exactly how they need it, when they need it.
There are options available, such as Bell Fuel & Tank Services or other companies that will partner with them to both solve existing fuel and tank storage problems (like microbial problems, water buildup and sludge or biomass present in storage tanks). The best fuel and tank services partners take a more comprehensive approach to fuel and PM care, bringing to the table the essential hybrid combination of
- Fuel testing (to pinpoint the specific problem)
- Mechanical fuel & tank cleaning (to address the issues that fuel chemicals aren’t always best at)
- Effective chemical treatments (because mechanical cleaning can’t keep problems away)
Anyone who relies on consistent stored fuel quality to get the job done would be well to keep this in mind.
Problem: Tank Sludge Buildup
Problem: Buildup in the bottom of storage tanks. Takes energy value out of fuel. Burns incompletely if drawn into the engine, leaves deposits.
Which change is it caused by? Cracked fuel instability, microbial destruction of fuel quality
Who might experience it? Those that store ULSD.
Preventive and remediative measures: Fuel stabilizers delay sludge formation. Effective stabilizers contain Antioxidant, Dispersant, and Metal deactivator components and should be effective with a treat rate below 1:2000. Using them early in the fuel's life prevents chain reactions; they can't reverse them after the fact. Anti-microbials can help by counteracting sludge from microbes. Opt for anti-corrosion tank treatments that also absorb sludge for dual benefits.
Problem: Microbial Contamination
Problem: Fuel & Tank Microbes (to prevent instability, filter plugging, tank corrosion)
Which change is it caused by? Removal of sulfur and aromatic from diesel fuel, yielding a fuel with less resistance to microbes.
Who might experience it? Those that store ULSD fuel and those that use fuel from infected tanks
Preventive and remediative measures: There’s a lot to be said for this, split into two categories.
Housekeeping – reducing conditions that might lead to microbial growth
For housekeeping measures to prevent microbial growth, control of water buildup in tanks is the biggest factor.
Existing microbes – essential steps to get rid of an existing problem
For existing problems, use biocides to kill microbes (water control additives won’t do it). You cannot kill microbes simply by removing water bottoms. You ESPECIALLY cannot get rid of a microbe problem through simple fuel polishing. YOU HAVE TO USE A BIOCIDE.
How to choose the right biocide
The best biocides should incorporate the following characteristics
- Broad spectrum
- Fast acting
- Long lasting kill rate
One thing to note is that all biocides get used up. No biocide lasts forever. 30-60 days is the industry best.
- Dual-phase (Water and fuel) effective rate
- Some chemisitries like Biobor are not effective in water.
- Must be registered with the EPA Pesticide division
If they don’t have an EPA registration number, they aren’t registered and it may be illegal to use it in your particular state.
We have a lot more information on best practices for solving these types of problems. If you or your customers think you may have this kind of issue, talk to us. We’ll be happy to help.
Proper Application of biocide Is Key
A biocide only works if it is applied properly.
- Prior removal of as much water as possible
You need to remove as much of the tank water as possible.
- Fuel circulation after biocide application is essential
After biocide addition, fuel circulation is essential, as biocides must come into contact with microbes for it to work.
- Wait >8 hours before using fuel
Biocides will take a certain time to work, so you must wait a minimum of 8 hours before using the fuel, to allow for complete kill and to allow dead microbial mass to settle. The dead microbes will still need to be filtered out.
Lastly, sometimes it’s worth considering a biomass dispersant to pair with the biocide to increase its effectiveness.
Filtration Considerations For Dealing With Fuel Contamination
Filtration Effectiveness: Filter Beta Ratings
In terms of particle filtration efficiency, beta ratio is still a quantitatively way to define filter medium effectiveness to keep diesel fuel relatively free of damaging aware particles. Beta ratios are defined as the ratio of the number of particles upstream to the number particles downstream at a specific particle size. Beta ratios unfortunately are often inadequate measures of fuel filter performance, being derived from standardized multi-pass fuel filter tests while on-vehicle filtration generally happens in one single pass.
Best Practice Recommendations For The Future: Questions You Need To Ask Yourself
Fuel Ready Question #2 – When’s the last time your fuel was tested?
Fuel Ready Question #3 – What can you expect if the fuel is bad?
Fuel Ready Question #4 – Have you checked for microbes?
Fuel Ready Question #5 – Do you know the difference between mechanical and chemical solutions? And which one is best for you?
Fuel Ready Question #6 – Do you have a partner to take care of the details if you’re not confident you can do it yourself?
Helpful Resources
Managing Fuel in 2018
Webinar
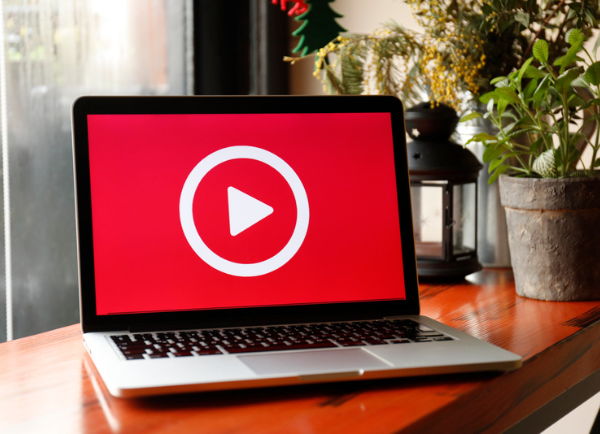
How to Prevent Diesel Fuel Fungus
Technical Sheet
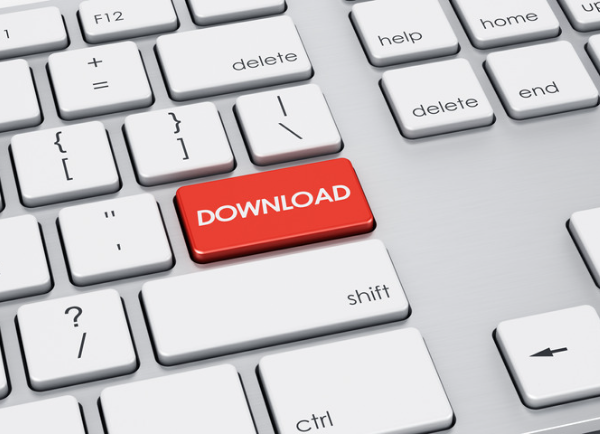
Could Half An Approach Be A 100% Mistake
Tip Sheet
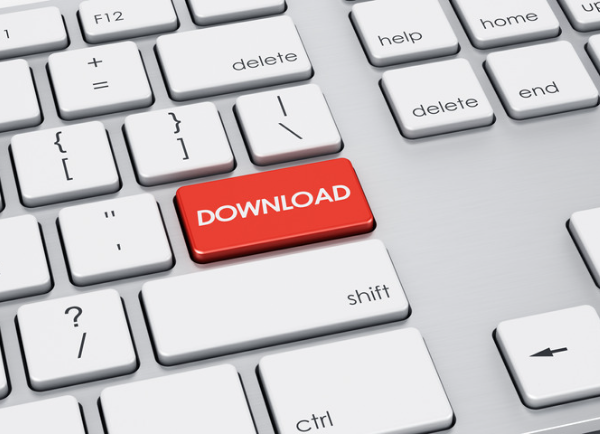
Fuel Tank Contamination Checklist
Checklist
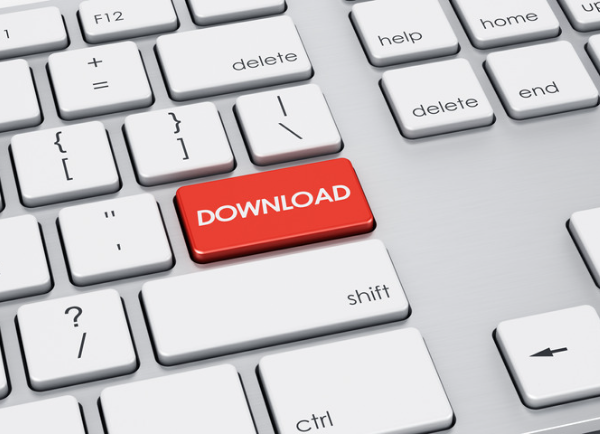
Fuels Aren't What They Used to Be
Whitepaper
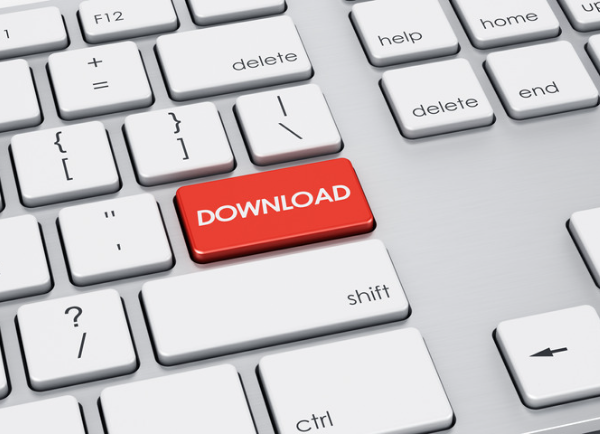
The Essential Fuel Tests That Fuel Polishers Need to Know About
Whitepaper
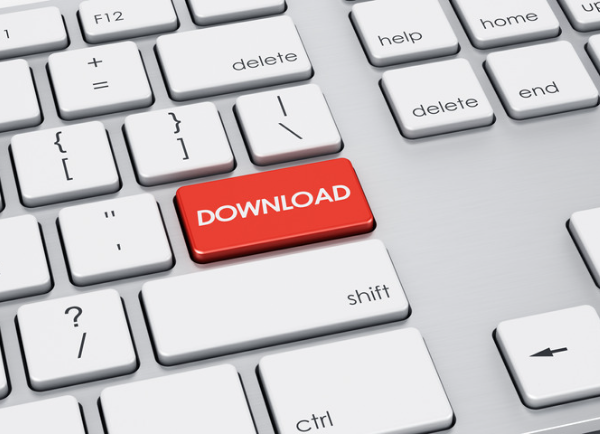
Fuel Changes and How They Affect You
Webinar
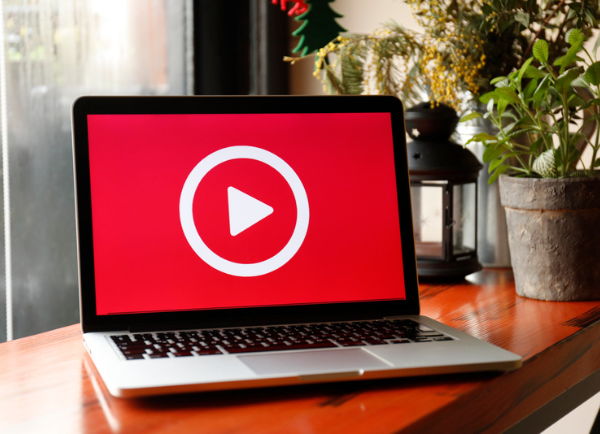
What's My Fuel Health Score?
Webinar
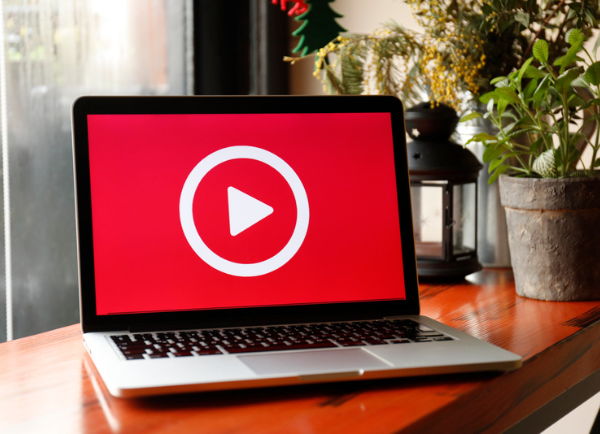
Fuel Checklist for Stored Fuels
Checklist
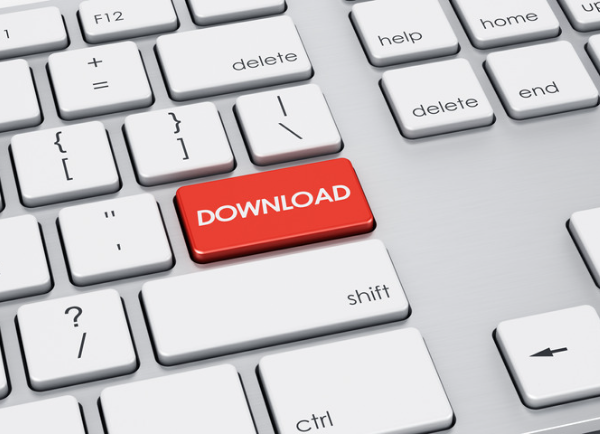
Fuel Storage on our Commercial Blog
2 min read
When Black Sludge Appears: Why Your Fuel Storage Strategy Needs an Overhaul
Erik Bjornstad: Aug 13, 2025
3 min read
The Hidden Cost of Biodiesel Instability: Why Your Storage Tanks Are Working Against You
Erik Bjornstad: Aug 5, 2025