Preparing Your Fuels For Hurricane Season
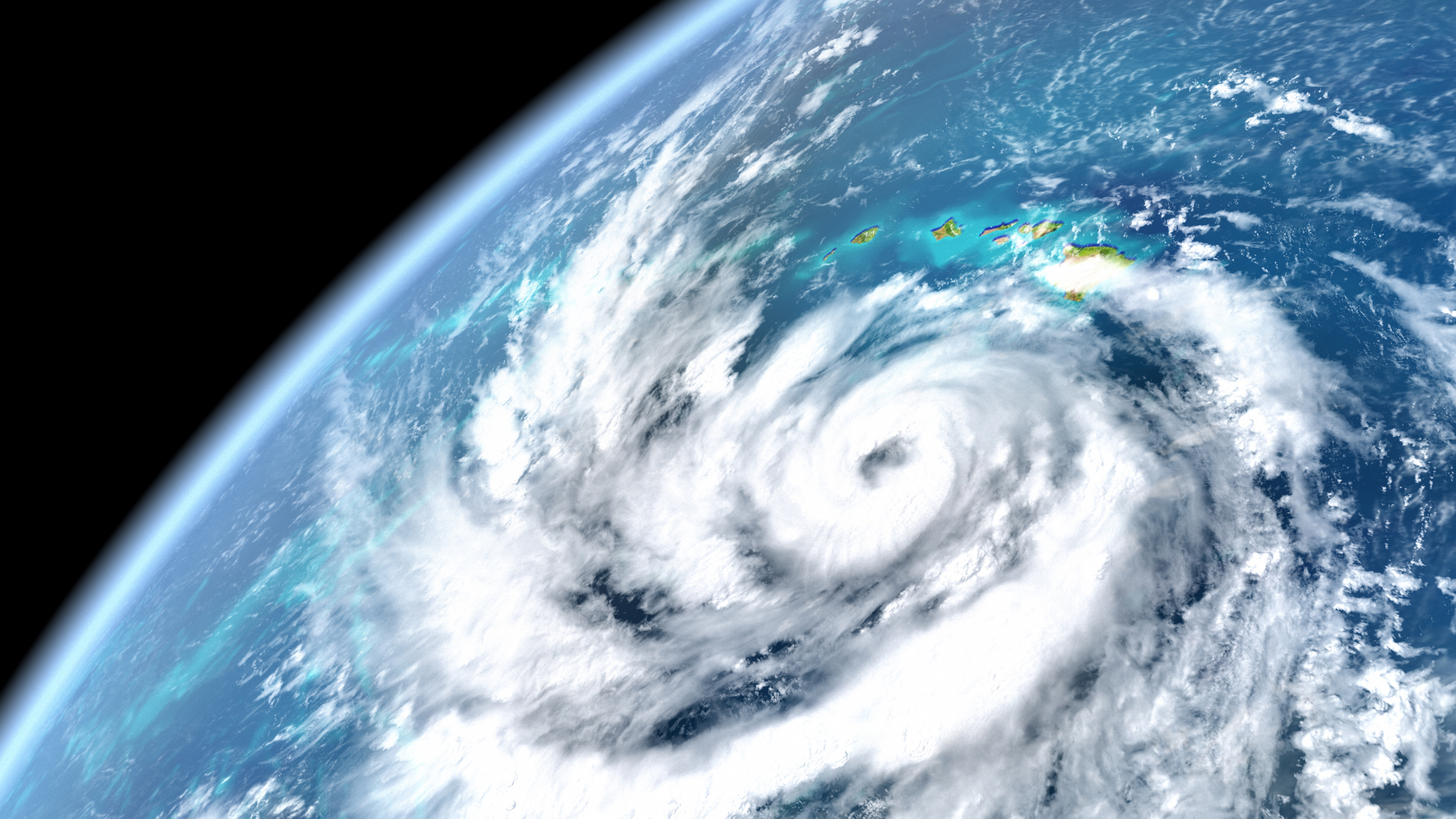
The Atlantic Hurricane Season typically runs from June through the end of November. If you work for any kind of municipal government or other large entity, you probably have a contingency plan in place dictating the actions to be taken to prepare for the arrival of a hurricane or large storm system.
Small and medium businesses, on the other hand, may not have such plans laid out. So we’d like to offer some supplemental helpful suggestions to help put together an emergency plan relative to the fuels you may have.
Reasons For Concern
Even though most people and entities think they’re adequately prepared for hurricanes and major storms, there are reasons for concern that they may not be as prepared as they want to think:
Time Isn’t Always On Your Side
It’s clear that you don’t get much warning with most hurricanes, which is why they can catch even the best fuel administrators off-guard. The State of Florida estimated a 12-hour notice is the best advance that people can expect, which is a troubling contrast to the fact that, even in a prepared state like Florida, some areas take 28 hours or more to execute tasks like evacuations.
Hurricane Frequency
Hurricane tracks of past storms show that most areas of coastal states can expect to be exposed to a hurricane at least every 25 years. Really, this seems way too long. And we all know what happened in 2004 and 2005.
Lack of Real Preparation
Over 80% of U.S. localities do have a formal disaster plan on-hand. But an audit by the International City Management Association concluded that local governments continue to be surprised despite having this in place. The audit also found that local governments often fail to improve their plans even after a disaster has been experienced in their area.
Why do they fail when they should know better? Most likely, a combination of a lack of relevant experience with the issue of disaster response, a failure to learn from experience, a lack of commitment to doing the work (which may not always have an immediate and visible payoff), and lastly, doing the wrong kind of planning (which may target the wrong areas).
The wrong kind of planning (or none at all) can be a death blow for businesses. Experience shows that for businesses who have to spend 30 days or more recovering from a hurricane or disaster, 80% of them go bankrupt. What is a common thread among these kind of businesses? They didn’t have a plan to prepare.
What About Your Disaster Plan for Fuels?
Let’s focus on the last reason – doing the wrong kind of planning. If you have one, your plan likely has procedures for how often you have to meet with various individuals in the chain of command, where emergency vehicles have to be moved to at what time, guidelines for evacuating designated groups of people, and assessment/allocation of available resources, both physical and human. Even if your disaster plan isn’t as lengthy as, say, City of Miami’s (48 page) short novel, you should expect it to cover those areas.
But the obvious fact is that in order to execute the steps of these kinds of plans - the evacuations and the transferring equipment/supplies to needed destinations, the providing of command centers with essential power - these all rely on having access to good fuel that works like it’s supposed to, when it’s most needed. If the fuel is bad, the other parts of the plan won’t fall into place very well, if at all.
- The 2003 Blackout - hit a large part of the country and affected 50 million people. Fully 20% of emergency systems put into place specifically to provide power in such an emergency failed to work because the fuel contained therein didn’t work.
- Superstorm Sandy (2012) – the well-publicized case of NYU’s Langone Medical Center and Bellevue Hospital having to evacuate critical care patients because their back-up generator systems failed.
- Hurricane Katrina – when 80% of New Orleans wasn’t being flooded by 20 feet of water, a significant number of backup generators simply failed to work, due to lax maintenance.
How Not To Be A Statistic
Consider these suggestions to supplement your emergency preparation plan. Hopefully your plan will already include some or all of these steps. These steps will ensure that the fuels you rely on to power your backup systems will do their job in your hour of need. The recommendations are grouped according to the decreasing time frame leading up to storm landfall.
5 Days to 72 Hours Before Landfall: Pre-Storm Activities
- Make sure fuel deliveries are scheduled to ensure fuel storage tanks are full as needed
- There’s less guarantee you’ll be able to get fuel the closer landfall-time comes
- Perform water housekeeping procedures and test stored fuel for bacterial content
- Microbial test strips don’t work very well, so consider ATP testing that gives you specific results in minutes, enabling you to make the right decision immediately, when you have the least amount of time to waste
- Treat stored fuel with biocide if microbial tests come back positive
- Top off the fuel in all essential vehicles
- Test and fuel backup generators
72-48 Hours Before Landfall: Pre-Hurricane Watch Activities
Hurricane watches most commonly start 48 hours before expected landfall.
- Performance fuel filtration for infested fuel with positive microbial tests as per earlier
- Run refueled generators after filling to ensure proper functioning with new fuel
- Top off fuel tanks and service all vehicles, portable and emergency generators, pumps, compressors and ventilators.
36 Hours Up To Landfall
- Test backup generators one final time
- Fuel all essential vehicles as needed
- Store and/or secure an extra supply of fuel if needed
Storm Landfall: The First 24 Hours
If you’ve followed the previous steps, you shouldn’t have to worry about fuel issues during that first 24-hour period when you’ve got plenty of other things to worry about.
Ongoing Preparations When All Things Are Quiet - Knock Out Microbes
When it comes to fuels, the success that you’ll have in implementing the above steps relies on the groundwork you lay during the “times of plenty” – when everything is fine and no storm is on the horizon. The best thing you can do on an ongoing basis is control the water buildup in your storage system and keep the microbes at bay.
You likely have water remediation steps you take regularly, but what about the microbes?
Microbial growth in fuel tanks definitely falls under the category of “better safe than sorry”. It’s much less stressful (and much less expensive) to prevent microbial growth in fuel tanks than to try eradicate an active infestation after it’s established. Especially when the infestation spreads to all areas of your fueling system.
Beyond proper water control steps like draining, the best thing you can do to prevent microbial growth is to periodically treat your tank system with a biocide. Once a quarter is a good interval, though if your housekeeping measures aren’t the greatest, it’s in your best interests to do it sooner, say every 2 month or 6 weeks.
What about ”maintenance doses” vs. “shock doses”?
Typically, there’s a 2x difference between these. People look at the lower maintenance dose and think that’s the best one to use. In reality, the best thing to do is periodically treat with a shock dose. The most common shock dose is 1:5000 or about 1 oz per 40 gallons (for us Americans). Even at that treat rate, tank biocide treatment is very cost effective. If you want to ensure the best chance of success with your fuels in the quiet times when there’s no storm expectation, periodic treat with a biocide is your best protection.
It’s also strongly recommended to get on an interval-based microbial test regimen. Even if you just test your storage tanks, say, twice a year, you’ll know with much greater certainty when a microbial problem is about to hit, and you can knock it out when you have the time to do so. But I don’t know how to test. Don’t worry about that, as there are companies (like Bell Performance) that sell all-in-one microbial test kits - you pull a sample and put in the bottle, package it up in the supplied box, and send it back to them. They take care of the testing, compile your report and send it back to you electronically. Better yet, they keep track of the trends so that you get a long term picture of the microbial levels specific to your system. Something to consider.
Choose The Right Partner If You Need Help
Sometimes, it’s helpful to have a partner that can guide you through this process, especially the process of ongoing preventive treatment of stored fuels. The best partner is your fuel supplier who, in an ideal world, would be equipped with the knowledge and the solutions to help you ensure you’re doing what’s needed to minimize the chance of problems down the road.
If you have to look beyond your fuel supplier, the right partner should combine the right amount of experience with access to the right solutions (both for testing and prevention), and should bring both of those to the table with a philosophy of ensuring that their priority is to turn you into the expert.